Supplier Benefits
We have established processes and systems in place to benefit our suppliers
How you’ll benefit as a supplier
The Group’s focus on innovation has led us to become the largest retailer in Africa. We are ahead of the retail game in many ways, but we know that our success is closely linked to our suppliers.
Stronger suppliers ensure a more secure supply chain that equates to cost savings that we can pass on to our customers. This understanding, coupled with our intention to build long-term relationships with our suppliers, incentivise us to use the means we have available to support our suppliers, and have led to many success stories so far.
As a Group supplier, you can expect support in the following ways:
PROCESS AND SYSTEMS
INFRASTRUCTURE
As a prominent retailer in Africa, our Group has established processes and systems in place that benefit our suppliers. These include:
QUALITY ASSURANCE
The aim of our quality assurance department is to:
-
Manage and administer the quality of suppliers’ products and services, while also providing food safety input to the supplier.
-
Ensure the production of safe foodstuffs and non-foodstuffs within RSA and non-RSA countries.
-
Identify and mitigate risks by ensuring that suppliers implement adequate controls which are verified by the assessment of their food safety and quality management systems.
-
Minimise the liability and risk of products supplied into the Shoprite Group’s supply chain, whilst also ensuring brand protection.
-
Provide a consistent national and international approach to the production of safe food to ensure consumer protection and confidence, in other words “due diligence”, in respect of the Consumer Protection Act.
PACKAGING
We work with our suppliers to improve packaging by identifying potential weaknesses that could result in product damage, considering the design and material to increase shelf life and thereby reduce food waste; increasing the recyclability of packaging materials; and highlighting the use of recycled materials. Shifting to sustainable packaging is one of the biggest ways in which we’ve made a positive change to minimise our impact on the environment.
GROWING PROGRAMMES AND TECHNICAL EXPERTISE ON FRESH PRODUCE
Freshmark sources from local suppliers where possible and has growing programmes to assist producers. This enables producers to obtain finance for their farming activities and to plan their planting and growing seasons.
Freshmark also shares technical expertise to the benefit of farmers and producers, and actively provides assistance on any challenge experienced by its suppliers.
FOOD WASTE
Globally, food waste receives a lot of attention, and through our collaborative approach, we aim to reduce food waste in our value chain. To this end, we enter into joint programmes with our suppliers to find innovative ways to reduce food waste. We have collaborated with industry stakeholders and the Consumer Goods Council of South Africa on the country’s first Food Waste Voluntary Agreement.
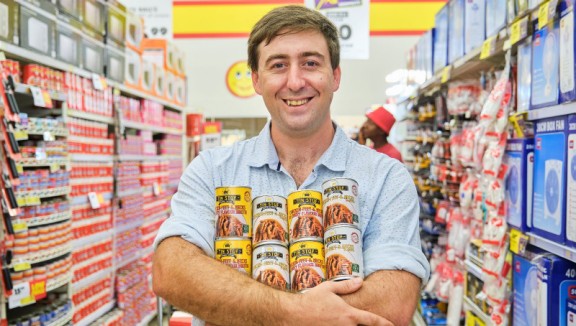
Eiren Drake, a 26-year-old entrepreneur supplies canned chicken feet and necks to Shoprite
Besides benefitting from the processes and systems already in place, Group suppliers also benefit from our African-wide infrastructure and distribution solutions. As a supplier, you can expect benefits like:
SAVING ON PACKAGING MATERIALS
We aim to reuse and recycle our packaging material, shifting to reusable packing crates all along our supply chain, and procuring more sustainable packaging options for our private label products.
We have also shifted to a circular economy model that supports as much reuse and recycling as possible, taking the economic, social and environmental impact of each product into account. In line with this thinking, all plastic waste from our stores and DCs are converted into pellets that are then used to make our shopping bags, and we also recycle cardboard through our DCs and have partnered with other retailers to reuse cardboard. Our trolleys and shopping baskets are made with at least 35% locally sourced recycled plastic.
Not only does this circular model reduce harm to the environment, it creates jobs in the recycling sector.
FOOD SAFETY SERVICES FOR MICRO, SMALL AND MEDIUM SUPPLIERS
Our team of food technologists assists and advises all micro, small and medium suppliers on legal compliance, food safety and quality assurance requirements. This means that our suppliers save costs while staying compliant.
Quality assurance requirements
Food business operators (including SMEs) are obliged to meet many responsibilities in terms of the products and professional services they introduce into their operations. These include meeting expectations for essential elements like:
-
Legislation, regulations and standards
-
Quality and food safety systems
-
Food safety assurance conditions
-
Contract conditions
-
Supply agreements
SAVING ON DISTRIBUTION
Our centralised distribution system allows access to a more efficient route to market than the traditional “direct-to-store” option where supplier vehicles drive extra mileage and waste time between individual store deliveries. In recent years, our investment in central distribution saved our suppliers billions of rands, most of which would have been spent on fuel alone.
Thanks to our centralised distribution model, suppliers do not need to tie-up their capital in warehousing and vehicles that offer no financial return; instead, they can focus on product development and production improvements.
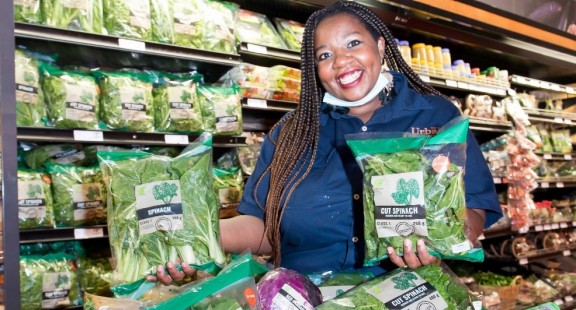
Nonhlanhla Mokoena-Chimhandamba, co-founder of Urban Grown. The 100% black-female owned company supplies whole and value-added lines to the Group’s fruit and vegetable procurement, buying and distribution arm, Freshmark.
Ready to apply?
We are always looking to expand the Group’s offering. If you have a product to sell or a service to provide, apply online and the relevant buying team will be in touch.